先上结论,微化工的风口已经若隐若现,尤其是今年 4 月山东豪迈推出了 12 万元的微反装置后大大降低了微化工的工艺研究门槛,导致更多的生产单位愿意投资进行微化工的研究。
在讲这个问题前现回顾一下微化工的历史和技术特点。
微化工的概念最早在上个世纪七十年代被一个德国人提出,名字我忘了,现在应该还活着。其主要的原理就是当流体通道减小之后可以产生一系列过程强化效应。
首先是传递效果的增强
任何化工的传递过程都要经过所谓的边界层进行传递,传递过程的快慢可以近似认为和边界层厚度呈反比。边界层的厚度目前是一个很难说清楚的概念,很难进行计算和模拟,但是有一个定性的结论就是边界层厚度绝对不可能大于流道尺寸,因此流道越小,边界层厚度越薄,传递过程越快。所以减小流道尺寸对所有传递过程,比如说传热(换热),液液传质(萃取),气液传质(气体吸收)等都有传质强化作用。这也就是微反应器中常常能比常规反应器中的反应速率明显加快的原因。
其次是微流道导致的传热界面增大
任何一个设备都有所谓比表面积的概念,尤其是涉及到传热过程。比如说在一个设备内反应放出多少热量,这与反应器内部装填了多少物料有关,反应放热同反应器的体积成正比。但是这些热量的移除却是与反应器面积相关的,因为热量传递依赖的是热交换表面进行的,换热面积越大传递的热量越多。为了维持一个反应器内部的温度恒定,反应放热与热量移除必须守恒。比表面积越大,反应器的散热能力越好,反应器温度越能维持稳定。如果我们假设反应器是圆柱体的话,反应器的比表面积与直径是成反比的。常规的反应釜,一般直径在 1000mm 左右,实验用的反应瓶直径 80-100mm,而微反应器直径最大不超过 1-3mm 也就是说,微反应器的移热能力是常规反应釜的 1000 倍。一些反应在反应釜力升温很快,是非常危险的反应,但是在微反应器总却可以成功进行。
第三是平推流动
常规的搅拌釜里的流动状态是全混流动,按照反应工程的角度来看这是一种低效的流动形式。为什么呢,因为绝大多数反应,反应底物浓度越高,反应越快速。全混状态下,反应器内的底物浓度永远等于出口浓度,而对于一般工艺要求,反应器出口浓度都是很低的,导致反应器整体在低浓度下运行,反应效率很低。而在管式反应器与微反应器总,流体在反应器内部近似呈平推流动,也就是说,反应器内浓度沿反应器轴向存在分布,进口高出口低,而出口浓度为反应工艺要求,这样的话反应器内的平均浓度式高于搅拌反应器的,这进一步提高了反应效率。
最后是可以进行数量放大
就是在微反应器的研发过程中可以通过数量放大实现工业化生产,这样工业生产条件和实验条件几乎完全相同,避免了在放大过程中产生的各种放大效应,整体的研发流程变短。
从上面这些有点来看,微反应器主要用于某些剧烈地化学反应,因为剧烈的化学反应放热都很明显,因此需要快速移除反应热,同时剧烈化学反应一般都容易生成副产物而在平推流状态下能够最大程度地抑制副反应的发生。 此外对于非均相的气液,液液,液固过程,由于其过程强化作用都能够有效地提高反应效率。
当然作为微通道反应器也有许多不足的地方,主要体现在以下几点。
1. 不能使用固体,这个很好理解,无论是催化剂颗粒还是反应产生的固体,都会堵塞孔道。目前一般认为,微通道内颗粒大小几十微米就是上限。
2. 压降大,液体通过微通道压降很大。当然这几乎是不可避免的,因为任何传质强化过程都是利用能量换效率的。
3. 设备大型化困难。现在的微反应器如果采用康宁路线单板通量应该在千吨 / 年左右,还是难以满足大宗产品的生产要求,微反应器目前的应用还是局限在高附加值的产品上。
再来说说微反应器目前的推广趋势。
按照技术特点来分析,我倾向于把微反应器分成两类:
1. 康宁路线:通过在板材上蚀刻或采用机械加工出超细小的通道作为微反应器,康宁公司原来也就是康宁玻璃厂,所做的工作就是在板材上雕刻出各种形状的微通道并且测试这些通道对反应的适应性。康宁路线主要的问题在于设备通量小,连康宁公司自己对设备的工业化都没有信心,在市场方向方面,他们将自己的反应器定义与适用于实验室工艺筛选的设备。至于工业化生产,据我所知单板的康宁路线反应器生产能力也就是在千吨 / 年左右。而要实现大规模生产,只能卖上几百套反应器并联起来。一套反应器系统的价格现在来看都属于天价,一般工厂是难以负担的。
2. 拜耳路线:拜耳路线是一种与康宁反应器截然不同的微反应器路线,其凸出的特点就在于,通量可以做的很大,是有希望达到工业级别产量的。但拜耳路线的微反应器结构有一个重大缺陷:换热能力不足,由于结构问题,拜耳微反应器换热效率约为康宁路线的 1/10,当然在很多条件下也够用了。但是一旦出现强放热反应,就必须做成多段绝热式反应系统,对工艺研究要求非常高。
从国内微反应器的推广来看,目前已经有几家企业在开始这方面的工作。从我同他们的交流来看,走康宁路线的有:豪迈,沈氏,大连微凯等。这几家单位中,豪迈和沈氏的加工能力完全没有问题。大连微凯设备加工能力最差,核心实验设备是买西门子的。豪迈在微反方面起步较早,基本上做到了设备和工艺齐头并进,宣传上也做的很好,最近推出了 12 万的微反小试装置很有可能大幅降低研发设备投入,产生一系列的新工艺。沈氏方面起步较晚,设备加工没有问题,但是工艺方面没有跟上。至于拜耳路线,我比较推崇清华大学,在这方面做得工作很多,已经有工业化的纳米碳酸钙生产案例。
最后再来说说微反应器的发展趋势,总结起来可以概括为以下几点:
1. 需求是肯定存在的
实际上目前已经有很多生产单位意思到了微反应器的价值,甚至在国内加工企业起步之前就花费巨资购买国外的小试设备。但是直到现在我没有看到有企业基于此类小试设备自主研发出工业化生产工艺的案例,国内仅有的几个工业化微反案例都是同清华大学甚至拜耳合作产生的。剩下的企业花了钱买了设备,发现做不下去了,设备就在厂房里一扔成了废铁。
2. 设备是可以加工的
初步接触微结构的人都会认为,微结构的加工对国内企业来说是一件非常困难的事情,长期以来在各种宣传中都认为目前国内的机械加工能力远远落后于欧美。但是实际上目前无论是康宁路线还是拜耳路线。就设备加工来看,国内的加工能力都是可以做到的,很多号称在做微反的企业确实可以进行设备加工,这个没有问题。
3. 工艺是有问题的
但是现在关键的问题还在工艺研发上,目前能做微反的企业充其量就是设备厂,不具备将工艺与设备结合的能力。即使对于康宁流派的微反应器,如何由现有工艺包过度到微反应器条件下的工艺包对于目前的微反研发企业来说都是一件困难的事情,更不要说工艺研发难度更大的拜耳微反应器。而拜耳微反应器才是可能进行工业化的正确路线。现在我们的问题就在于:工艺包有,设备也有,但是工艺与设备的结合做不到。工艺在生产企业手中,设备在微反加工单位手里,出于技术垄断和商业方面的考虑,这两方不会进行充分的技术交流。
4. 前景是光明的
当然随着技术的发展,这些都不是问题,从现在来看现状确实有渐渐打破的趋势,现在一套微反小试装置的成本已经降低到几十万,一般的生产机构都有能力负担,将会有越来越多的企业具备微反应器研究能力,结合他们的工艺能力,即使只有很少一部分工艺包适宜采用微反应器,应当很快就会有可工艺生产的项目出现。此外微反应器生产商在工艺研发的人员投入上也在加大。这两方只要有一边打破平衡,微反应器的风口就会出现。
写到这里其实我还想说明一个问题,就是微通道反应器的必要性,微通道反应器众多优点,将反应,放热都得到了强化。但实际上这些优点普通的管式反应器也具备,当然效果不如微反应器明显。比如说,一台 DN15 的反应管道,其传热效果就会比搅拌釜好几十倍,同时具有平推流的特点,反应器压降还远小于微反。这些优点足以在产品的更新换代中被很多企业接受。实际上我认为如果要给反应器像武器一样划分代差的化。普通搅拌釜算一代,管式反应器等其他传统强化设备算第二代,微反应器算第三代。实际上第二代反应器就比第一代反应器具备很多明显优势,但实际上我国的大多数化工生产还停留在第一代的水平上。现阶段工艺技改,只要用二代反应器替代一代反应器就能见效益。但是偏偏这一步我们都没有做出来,我一直说我们的生产工艺与设备的结合能力差。比如说某氨解反应,易燃易爆,德国人 40 年代就用管式反应器做,效果很好,但是我们直到现在还在釜里搅来搅去,几乎每个做这个产品的厂都炸过。说道底,反应工程能力不过关。从第一代反应器到第二代反应器,如何进行工艺与设备的结合,这门课我们是一定要补的。当然微反应器有可能给了我们一个跨越式发展的计划,我们可以迈过管式反应器等其他反应设备,直接接轨国际最先进的反应器,这确实是一个好时机。
最后夹带一点私货,不要认为微反应器很难加工,把微反应器想的很遥远,下面这张图就是我自己做的微反应器冷模装置,已经具备了拜耳微反应器的特征,孔道直径已经到了 0.2mm,通量已经达到 1400 吨 / 年。当然因为加工能力的限制,压降比一般微反应器大,材质问题只能做萃取。全套设备加工没用什么高端设备,一套下来 2000 以内搞定。所以微反应器真的就在我们身边。
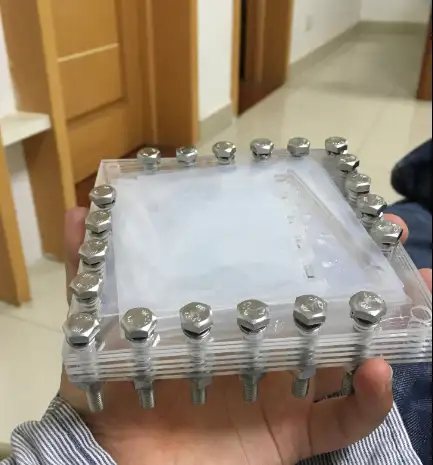